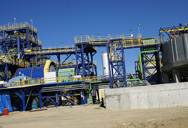
Ball mill - Wikipedia
A ball mill is a type of grinder used to grind, blend and sometimes for mixing of materials for use in mineral dressing processes, paints, pyrotechnics, ceramics, and selective laser sintering. It works on the principle of impact and attrition: size reduction is done by impact as the balls drop from near the top of the shell.
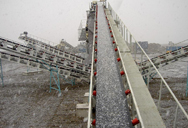
Ball Milling - an overview | ScienceDirect Topics
Ball milling technique, using mechanical alloying and mechanical milling approaches were proposed to the word wide in the 8th decade of the last century for preparing a wide spectrum of powder materials and their alloys. In fact, ball milling process is not new and dates back to more than 150 years. It has been used in size comminutions of ore, mineral dressing, preparing talc powders and many ...

Ball Mill: Operating principles, components, Uses ...
Several types of ball mills exist. They differ to an extent in their operating principle. They also differ in their maximum capacity of the milling vessel, ranging from 0.010 liters for planetary ball mills, mixer mills, or vibration ball mills to several 100 liters for horizontal rolling ball mills.
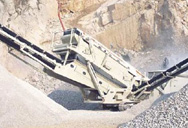
Ball Mill Features,Technical,Application, Ball Mill ...
Ball mills are used primary for single stage fine grinding, regrinding, and as the second stage in two stage grinding circuits. According to the need of customers, ball mill can be either wet or dry designs. Ball mills have been designed in standard sizes of the final products between 0.074 mm and 0.4 mm in …
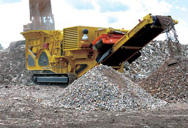
Ball Nose Milling Strategy Guide - In The Loupe
26-06-2017 · Ball Nose Milling Without a Tilt Angle. Ball nose end mills are ideal for machining 3-dimensional contour shapes typically found in the mold and die industry, the manufacturing of turbine blades, and fulfilling general part radius requirements.To properly employ a ball nose end mill (with no tilt angle) and gain the optimal tool life and part finish, follow the 2-step process below (see Figure 1).
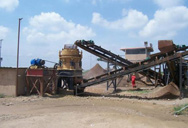
Ball Milling - alpha.chem.umb.edu
Planetary ball mills 9 . Vibration Mills 10 . Mixer Mill MM 400 11 Feed material: hard, medium-hard, soft, brittle, elastic, fibrous Material feed size: ≤ 8 mm Final fineness: ~ 5 µm Setting of vibrational frequency: digital, 3 - 30 Hz (180 - 1800 min-1)
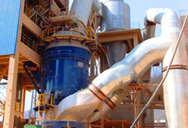
Laboratory Ball Mill - YouTube
01-07-2017 · https://www.911metallurgist.com/equipment/laboratory/comminution/mills/laboratory-ball-mill/ A Laboratory Ball Mill, because the calibrated grinding energy m...
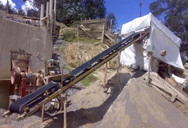
Ball mill - SlideShare
24-04-2015 · Ball mill consist of a hollow cylindrical shell rotating about its axis. Axis of the shell horizontal or at small angle to the horizontal It is partially filled with balls made up of Steel,Stainless steel or stone Inner surface of the shell is lined with abrasion resistant materials such as Manganese,Steel or stone Length of the mill is approximately equal to its diameter Balls occupy about ...
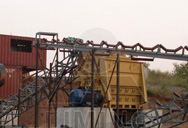
Mechanical alloying - Wikipedia
Mechanical alloying (MA) is a solid-state and powder processing technique involving repeated cold welding, fracturing, and re-welding of blended powder particles in a high-energy ball mill to produce a homogeneous material. Originally developed to produce oxide-dispersion strengthened (ODS) nickel- and iron-base superalloys for applications in the aerospace industry, MA has now been shown to ...
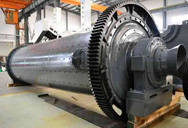
Mill sizing method - thecementgrindingoffice.com
Please find below two calculators for sizing mills using the Bond and Rowland methods: Ball mill sizing: Calculator for ball mill(s) in a single stage circuit. Rod ball mill sizing: Calculator for rod mill(s) as first stage of the circuit and ball mill(s) as second stage of the circuit.
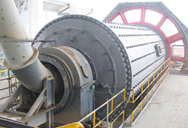
Ball Milling The Role of Media and Bead Mills - BYK
Ball milling is a grinding technique that uses media to effectively break down pigment agglomerates and aggregates to their primary particles. Using a rotor or disc impeller to create collisions of the grinding media, the impact and force created by the bead mills collisions break down the pigment agglomerates.
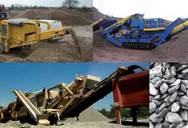
Practical modern techniques for the design of …
The technique has been sucessfully applied to a number of actual crushing and ball mill circuit design problems. Similar laboratory breakage tests are being developed with the objective of specifying breakage parameters for autogenous and semi-autogenous mill models.
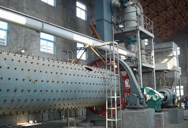
Ball Mills Selection Techniques - used hoist for salE
Ball Mills Selection Techniques. 7/30/2015 0 Comments Power plants, cement ball mill liner material, ought to choose those with higher carbon content of Cr-Mo steel or high metal forged iron materials and therefore the like. A problem to notice here is "conditions apply" construct.
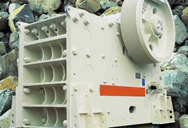
Overview of milling techniques for improving the ...
01-07-2015 · Ball milling is another popular size reduction technique used for the production of microparticles, especially in research laboratories. Fundamentally, a ball mill comprises a vessel or vial filled with balls, or rods, constructed from a variety of materials such as ceramic, agate, silicon nitride, sintered corundum, zirconia, chrome steel, Cr–Ni steel, tungsten carbide or stone polyamide ...
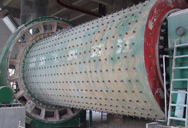
Lead recovery from PbZrO3 using wet ball-mill …
30-06-2006 · Lead recovery from lead zirconate (PbZrO(3)) ceramics was investigated using a wet ball-mill treatment in H(2)SO(4) aqueous solution. Subsequently crystalline alpha-zirconium phosphate (alpha-Zr(HPO(4))(2).H(2)O) was synthesized using a hydrothermal technique in order for the resource recovery of zirconium in the wastewater after the wet ball-mill treatment.
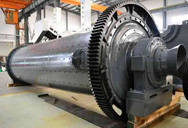
Fine Refining Ball Mill – Royal Duyvis Wiener B.V.
The ball mill is easy to maintain as all wear parts are manufactured from high grade materials and are easily accessible for replacement. The design of the vessel, shaft pin configuration, and ideal parameter control, make this ball mill the most efficient in today’s market.
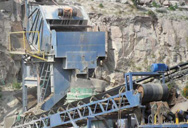
Industrial Ball Mills: Steel Ball Mills and Lined Ball ...
Ball Mills Steel Ball Mills & Lined Ball Mills. Particle size reduction of materials in a ball mill with the presence of metallic balls or other media dates back to the late 1800’s. The basic construction of a ball mill is a cylindrical container with journals at its axis.
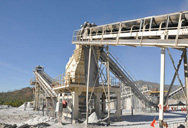
SAG/Ball Mill Optimization | KnowledgeScape
SAG/Ball Mill Optimization. Home | Plantwide Solutions | SAG/Ball | Flotation | Crush & Convey | Thickener | Froth Camera Systems | Conveyor Image Analysis. Better efficiency, starts with better grinding. You’ve already gone through the work to bring the ore to the mill, now it’s time to recover as much precious metal as possible.