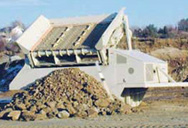
Cement Production: Raw Meal Production in Steps
The key word is quality! And this quality is achieved during cement production with exactly matched process steps. In the first stage, the raw meal is produced, as described below. Schenck Process measuring and feeding devices play a major role in this process. 1. Raw material production The raw meal is based on limestone which is mined at a quarry, crushed and temporarily stored in blending beds.
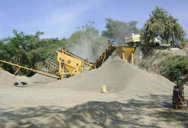
Raw materials for cement manufacturing
The second important raw material for cement production is clay.The main component of clay is formed by hydrous aluminium silicates.The stone composition of clay may vary from those close to the pure clay, to that containing a significant amount of admixtures as iron hydroxide, iron sulfide, sand, calcium carbonate, etc. Clay is used as an argillaceous component of raw mix.
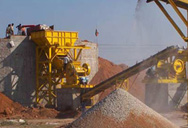
contents of raw meal in cement industry - …
Introduction of pneumatic blending silos for raw meal , 131 Raw materials Cement making is essentially a stone process industry and has much in common with... Raw Meal Preparation Know More. Grinding the raw material with both horizontal and vertical mills requires vast amounts of energy As a result, the main challenge in the grinding process is to .... Re: Raw meal to clinker ratio Know ...
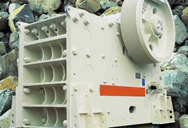
Cement Raw Mill in Cement Plant for Cement Raw …
Cement raw meal is a mixture of various raw materials before cement calcination. It is a mixture of lime raw material (mainly composed of calcium carbonate), clay raw material (aluminosilicate containing alkali and alkali soil) and a small amount of calibration raw material in a certain proportion and ground to a certain fineness.
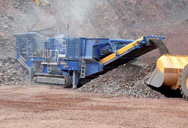
Raw Material Preparation Cement Mill …
Cement Raw Meal Grinding. Raw material preparation From the quarry to raw meal feeding into the preheater A company of Polysius ThyssenKrupp Technologies tk 2 Futureoriented raw material preparation solutions made by Polysius Innovative Individual Ideal The manufacturing of cement begins with the extraction and preparation of raw material a process covering the stages from raw material ...
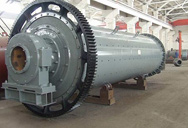
Raw materials - Cement
The most common raw rock types used in cement production are: Limestone (supplies the bulk of the lime) Clay, marl or shale (supplies the bulk of the silica, alumina and ferric oxide) Other supplementary materials such as sand, fly ash/pulverised fuel ash (PFA), or ironstone …
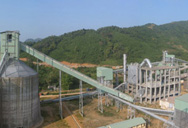
Raw material preparation. From the quarry to raw meal ...
Depending on its characteristics, the raw material needed for the cement production process is quarried by blasting, hydraulic excavators or ripping. A wide range of crushing plants – depending on the material’s properties and type of extraction – can be used for breaking the extracted raw material to the size required by the raw mill.
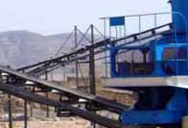
Manufacturing process | Lafarge - Cement, …
The cement manufacturing process starts from the mining of raw materials that are used in cement manufacturing, mainly limestone and clays. A limestone quarry is inside the plant area and a clays quarry is as far from the plant area as 25 km. The limestone is excavated from open cast mines after drilling and blasting and loaded onto dumpers which transport the materials and unload into hoppers …
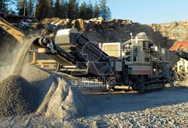
Cement Clinker Quality Control During Clinker …
During normal production process, the clinker is always calcined in a fixed temperature range. According to the fluctuation of raw meal composition, the calcination temperature of clinker is generally between 1350℃ and 1450℃. If the temperature in the kiln is too low, it is easy to produce underfired clinker.
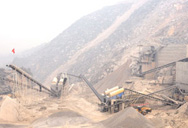
Cement Manufacturing Process | Phases | Flow …
30.08.2012 · Cement Manufacturing Process Phase 1: Raw Material Extraction Cement uses raw materials that cover calcium, silicon, iron and aluminum. Such raw materials are limestone, clay and sand. Limestone is for calcium.
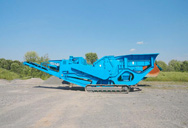
The cement kiln
The basic dry process system consists of the kiln and a suspension preheater. The raw materials, limestone and shale for example, are ground finely and blended to produce the raw meal. The raw meal is fed in at the top of the preheater tower and passes through the series of cyclones in the tower. Hot gas from the kiln and, often, hot air from the clinker cooler are blown through the cyclones. Heat is …
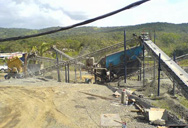
Raw Mill In Cement Production In Russia
Egypt Cement Plant Vertical Mill Coal Russian In the cement production line producing 1 ton of Cement need grind at least 3 tons of materials including raw materials fuel clinker mixed materialsgypsumGrinding operation consumes about 60 of total power in cement plants raw material grinding more than 30 while coal mill used in cement plant consumes 3 cement . Home; About us; …
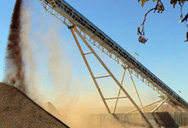
Cement Production | Apache Cement | Shwe …
The minerals needed to produce cement (calcium carbonate, silica, alumina, and iron ore) are extracted from limestone, mudstone, red clay and laterite from relevant raw material quarries by …
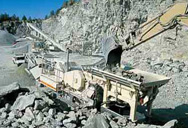
Cement Raw Mill Based On Pcs And Profibus …
Cement Raw Mill Based On Pcs And Profibus Production Line. 2020-7-13of Wonder Cement. The answer was Cemat-based optimization solutions. Cemat, a part of the Siemens Sicement product family, is based on Simatic PCS 7, a proven distributed control system featuring unique open Cement MineralsFocus 32014 To enable automatic and hands-free plant operation, Siemens installed an.
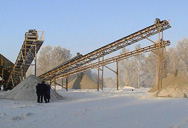
Parametric Studies of Cement Production Processes
The cement manufacturing process starts by handling a mix of raw materials: (i) naturally occurring limestone, which is the source of calcium, (ii) clay minerals and (iii) sand, which are the sources of silicon and aluminium, and (iv) iron-containing components.
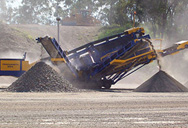
Raw meal and secondary fuel metering in the …
01.09.2009 · Raw meal and secondary fuel metering in the cement industry 1 Rotary vane feeders with CR coating, (ZS XXL 900 x 1000, overall height 1200, T product = 400 °C) 2 Inside view (ZS XXL 900 x 900 mm, overall height 1200 mm) 3 ...
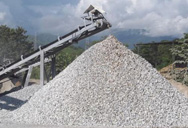
Cement Production: Focus on what really counts | …
Whether you are managing a project, automating a fuel handling system, selecting instruments for your clinker process or packaging a NOx gas cleaning solution for your environmental compliance program, our experienced process automation consultants can handle all measurement and control requirements of fully-integrated cement plants: Raw meal ...
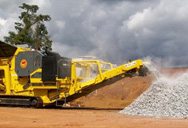
Clinker Production - an overview | ScienceDirect …
Arthur Michael Harrisson, in Leas Chemistry of Cement and Concrete (Fifth Edition), 2019. 4.2.2.3 Blastfurnace Slag. Where it is not appropriate to use blastfurnace slag as a cementitious material, the composition and origin of slag provides a potential raw material for clinker production.Most raw materials for cement manufacture are quarried and prepared for firing in the cement kiln at a cost.
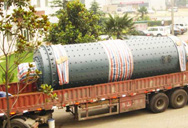
Raw meal silo – level measurement and point …
Cement silo; Cyclone; Silo for solid fuels; Tank for liquid fuels; Crusher; Conveyor belt transfer station; Conveyor belt; Truck loading; Diesel tank; Raw meal silo Level measurement and point level detection in raw meal silos. Radar, Vibration. Guided Wave Radar, Vibration. Process data. Measuring task: Level measurement and point level detection. Measuring point: Silo. Measuring range up to ...