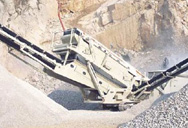
Surface texture formation mechanism based on the ...
01-09-2020 · Research on the process mechanism of ultrasonic vibration-assisted grinding had been carried out by some researchers. H. Wang et al. [] studied the material removing process, single stone trajectory model, and tool-workpiece interactions considering many process parameters with elliptical ultrasonic vibration-assisted grinding.Cutting force model was conducted and verified by …
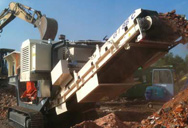
Vibration Grinding Process Monitoring - salabv.nl
Vibration Grinding Process Monitoring - odanahschool.org "Vibration monitoring of a gear grinding process" by ... Gear grinding is a process used to improve the surface finish of machined gears to increase their lifespan and decrease noise during their operation.
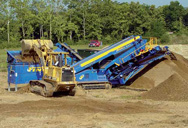
Condition monitoring of gear grinding processes
process are chatter vibration, grinding burning and surface roughness deterioration.These anomalies should be identified as soon as possible in order to maintain the desired workpiece quality. In this paper, the analysis is concentrated on the gear grinding. The grinding process depends on the tool performance, on the machine
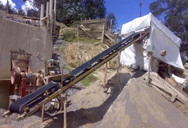
Grinding Chatter and Vibrations | SpringerLink
Grinding is also viewed as an unpredictable process because of the large number of variables involved and inadequate understanding of the relationships between those variables and the grinding process performance. That is particularly true of vibration in grinding operations, commonly referred to as grinding chatter.
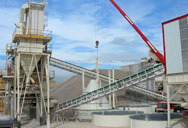
How to Reduce the Effect of Vibration in …
In a production-grinding operation, waviness on the part surface is a potential clue that the machine or process has developed a vibration problem. The effect might be seen in inspection, or if there is a lapping or polishing step, more time might be spent during that step removing the waves.
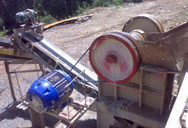
Effect of grinding forces on the vibration of …
01-11-2000 · Forced vibrations are caused by periodic disturbance external to the grinding process. Such external sources of disturbances may be caused by factors affecting the spindle system such as out-of-balance shaft, bearing variable compliance vibration, …
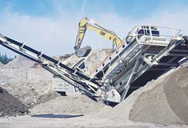
Vibratory Finishing - Vibratory Grinding - We finish …
Vibratory finishing – a universal process for different components. Large or small, light or heavy, individual pieces or series numbers beyond the million mark: No matter how different your components and requirements may be – in vibratory finishing, a wide variety of components can be deburred, rounded, polished and smoothed.
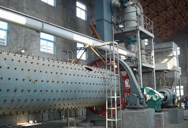
Grinding (abrasive cutting) - Wikipedia
Grinding is an abrasive machining process that uses a grinding wheel as the cutting tool.. A wide variety of machines are used for grinding: Hand-cranked knife-sharpening stones (grindstones)Handheld power tools such as angle grinders and die grinders; Various kinds of expensive industrial machine tools called grinding machines; Bench grinders
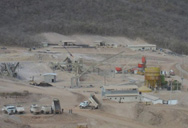
Basics of Grinding - Manufacturing
grinding machines perform the dressing task automatically. The application of coolants to the grinding process is important. Coolants reduce grinding machine power requirements, maintain work quality, stabilize part dimensions, and insure longer wheel life. Coolants are either emulsions, synthetic lubricants or special grinding oils.
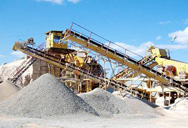
5Tips of Vibration Analysis in Grinding …
Tips of vibration analysis in grinding machines. When precision dies grinding, it is very difficult to solve the problem of vibration of the grinding machine. Because the vibration of the machine tool directly affects the effect of the dies processing. For example, the surface finish is poor.

Development of Control System for Vibratory …
However, in grinding vibration (Chatter) between wheel and workpiece poses challenges in maintain ing process requirements. A wide range of investigations have been carried out to detect and av ...

What We Do - Accretech SBS
In order for the wheel of a grinding machine to accurately cut, produce smooth surface finishes, and generate correct part geometry, it is necessary to prevent vibration in the grinding process. A primary cause of vibration during grinding is the existence of imbalance in the grinding wheel. This is often due to the heterogeneous nature of the ...
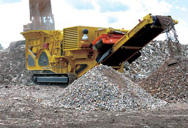
Performance Enhancement of Grinding Processes Mutual ...
be maintained in the grinding process, no vibration or chattering should be allowed during the process. Degradation of workpiece contour and roughness due to vibration in grinding can be more severe than that caused by vibration in machining. Vibration generated in grinding is classified into two

Chatter Vibration Monitoring in the Surface Grinding ...
Proceedings 2018, 2, 126 4 of 5 Figure 1. Picture of the workpiece surfac e after the grinding process (a) without image processing and (b) with image processing; (c) vibration signal during the grinding process.In Figure 2a, three frequency spectra are shown: for the entire vibration signal, for the section

Vibration characteristics of golf club heads in their ...
To control vibration-induced white finger among workers performing the fine grinding of golf club heads, the aims of this study are to clarify the major vibration sources in the grinding process, to identify and understand the basic characteristics of the club head vibration, and to propose potential approaches for reducing the vibration exposure.
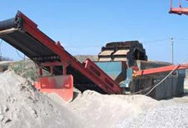
Vibration monitoring of a gear grinding process
final quality. The objective of this research is to identify how process parameters during the gear grinding process vary and determine if they can predict the noise associated with gears in final assembly. Specifically, this research records the vibrations on the grinding wheel and decomposes them using a Fast Fourier Transform (FFT).
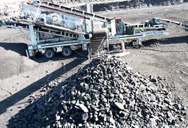
(PDF) Condition monitoring of gear grinding …
process are chatter vibration, grinding burning and surface roughness deterioration.These anomalies should be. identified as soon as possible in order to maintain the desired workpiece quality.
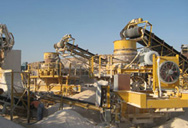
New Technologies for Vibratory Grinding | General …
Grinding can be done in batches, or in a continuous flow process (which is more common). First, material enters one end of a vibratory grinding mill drum into horizontal cylinders. Then, the mill uses a vibratory motion to mix and grind the particles, with operating speeds ranging from 800 to 1500 rpm.
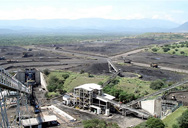
grinding machine, vibration, chart, severity
flowchart of the process of manufacture of the zinc sulphate 2020-09-03; commercial micro pulveriser for grinding garam masala 2020-09-03; ... grinding machine, vibration, chart, severity , CGM grinding plant grinding machines are available in a wide variety of designs, sizes and power capaciti...