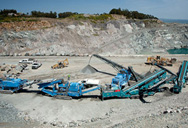
Grinding Process In Cement Manufacture
Grinding Process In Cement Manufacture; Cement Manufacturing Process: What is Cement made of. Methods of Manufacturing Process of Cement. At present Portland Cement is manufactured by two processes, Dry Process, and Wet Process. The main difference between these two methods of manufacturing of cement is that in the dry process, calcareous and argillaceous raw materials are fed …
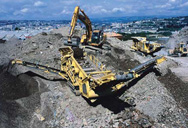
grinding process in the production of cement - …
Cement Grinding - Mineral Processing & Metallurgy. The principle ofGrate Discharge grindingis nearly universally adapted in the cement grinding industry.Grate Discharge Ball Millsare the rule rather than the exception.Rod Millsfor raw and finish grinding begin to enter the picture. Larger and larger diameter mills become common. Lengths tend to ...
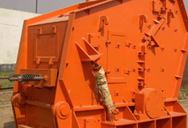
Efficient processes for grinding and separation - …
In the cement manufacturing process, cement grinding accounts for approximately 40 % of the specific electrical energy requirement. Two-compartment ball mills operating in closed circuit comprise the primary technology for grinding cement. The highest potential for energy savings and best operation occurs when these mills are equipped with perfect internals. Therefore, Christian Pfeiffer has ...
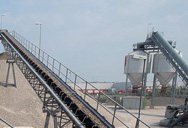
Cement Grinding Process Control
Cement Grinding Process Control; Cement mill Wikipedia. Temperature control. Heat generated in the grinding process causes gypsum (CaSO 4.2H 2 O) to lose water, forming bassanite (CaSO 4.0.2-0.7H 2 O) or γ-anhydrite (CaSO 4.~0.05H 2 O). The latter minerals are rapidly soluble, and about 2% of these in cement is needed to control tricalcium aluminate hydration. If more than this amount forms ...
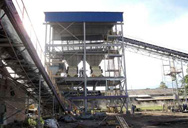
Grinding Machining Process : Complete Notes - …
Grinding Process: Mechanism of Grinding: In the grinding process, a layer of abrasive is responsible for removing the material from the work piece. As machining starts, the abrasives of grinding wheel and work piece comes into contact and due to the rubbing force the initial layer from the grinding wheel is worn out and a fresh layer of the abrasives involve in machining this process is ...
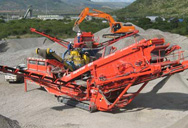
TYPES OF GRINDING PROCESS - Mechanical …
There are mostly four types of grinding processes used in industries and these are as mentioned here, we will discuss each type of grinding process in details here. Cylindrical grinding Object will rotate around one axis and the surfaces of object which need to be grinded will be in concentric with that axis around which workpiece will rotate.
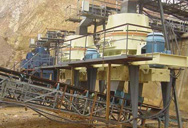
Innogrind - Grinding Process Management
Monitoring & Maintenance. INNOGRIND’s total solution includes the monitoring and maintenance of your grinding process. Regular inspections and maintenance will eliminate the most frequent causes of failures, but also minimize costly downtime.We monitor and document your process time, so that real-time and historic data are used to fine-tune your process for exceptional performance.
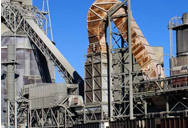
Frequent problems during grinding – grindaix …
Grinding is a widespread production process and has long been a fixed part of almost every industrial production environment. During grinding, the parts (workpieces) are literally given the “final polish”. Grinding operations thus contribute greatly to the quality of the finished workpiece. However, problems can often occur during the grinding process.
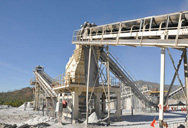
Grinding (abrasive cutting) - Wikipedia
Grinding is an abrasive machining process that uses a grinding wheel as the cutting tool. A wide variety of machines are used for grinding: Hand-cranked knife-sharpening stones Handheld power tools such as angle grinders and die grinders Various kinds of expensive industrial machine tools called grinding machines Bench grinders Grinding practice is a large and diverse area of manufacturing and toolmaking…
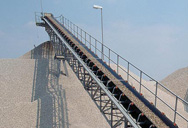
Grinding Parameters | SpringerLink
25.05.2018 · The grinding process is a geometrically undefined cutting process due to the undefined number and geometry of cutting edges interacting with the workpiece. The load on the workpiece as well as the load on the grinding wheel is a result of the programmed actuated variables, the cutting tool properties, and the workpiece properties. Due to the complex interrelationships in the …
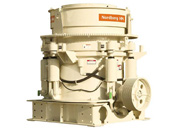
Cement mill - Wikipedia
The grinding action employs much greater stress on the material than in a ball mill, and is therefore more efficient. Energy consumption is typically half that of a ball mill. However, the narrowness of the particle size distribution of the cement is problematic, and the process has yet to receive wide acceptance. High-pressure roll presses
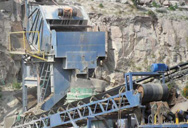
Grinding Cement Cement Mill Process Grinding …
Grinding Cement Cement Mill Process Grinding Mill Plant; Cement mill Wikipedia. A cement mill (or finish mill in North American usage) is the equipment used to grind the hard, nodular clinker from the cement kiln into the fine grey powder that is cement.Most cement is currently ground in ball mills and also vertical roller mills which are more effective than ball mills.
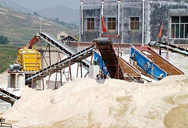
The back-end process: Step 3 – Wafer …
With a 2000 grit grinding process, the stress required to break the die was 50 percent higher than the stress needed to break a die with a (larger) 1200 grit grinding process. Figure 2 shows the method of applying the test force to the die, and Figure 3 shows the difference in the scratches on the wafers using different grits to grind the silicon. Sources of Stress. The amount of stress that ...
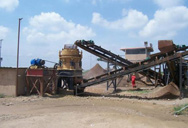
Grinding Machine: Types, Parts, Working & …
In this type of grinding process, the grinding wheel is maintained exactly the same shape as the final product. When the stone is passing through it automatically the pre-determined shape is formed on the workpiece. Wet and Dry grinding operation: Although there are two methods of doing a grinding operation, one is wet grinding and the second one is dry grinding. Wet grinding: In wet grinding ...
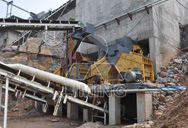
Effect of Moisture Content on the Grinding …
Grinding is a staple size-reduction process to produce stone powders in which the powdered form is chemically and microbiologically stable and convenient to use as end products or intermediate products. The moisture content of stone materials before grinding is a particularly important factor, since it determines the materials’ physical properties and the powder properties, such as flowability ...
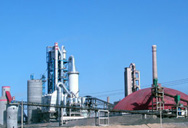
Cement Grinding Unit Process In India
cement grinding unit process in india. Cement Grinding Unit in India. Grinding occurs at the beginning and end of the cement production process. About tons of raw materials need to produce 1 tons of finished cement. Most of the grinding systems are either open circuit or closed circuit. For example, an open solution is used to adjust the feed rate of the feed clinker to achieve . List of 10 ...
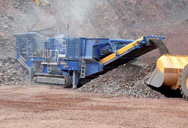
Grinding aid composition and cement product - …
Grinding aid composition and cement product . United States Patent 5429675 . Abstract: A grinding aid composition suitable for grinding clinker into hydraulic cement powder, an improved grinding process and an improved cement product are disclosed. The grinding aid composition is composed of a mixture of at least one alkylene ether glycol and particulate carbon. ...
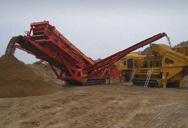
Cement Grinding Mill Process
Cement Grinding Mill Process. Cement mill grinding process cement mill great wall corporation. features the cement mill is mainly used to grind cement clinker in cement production process and it also applies to grinding various ores and other grindable materials in industrial and mining enterprises such as metallurgical plant stone plant and power plant and so onour company has more than 40 ...