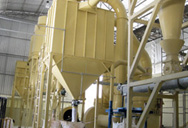
Tue Cement Raw Material Grinding Mill Table
Tue Cement Raw Material Grinding Mill Table. We are a large-scale manufacturer specializing in the production of various mining machinery, including different types of sand and stone equipment, powder milling equipment, mineral processing equipment and building materials equipment. They are mainly used to crush coarse minerals such as gold and copper ores, steel, iron, glass, coal, asphalt ...
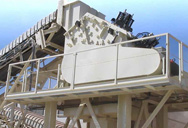
Cement Raw Material Grinding Mill Table - Lilith …
Cement Raw Material Grinding Mill Table. Raw mix is stored in a pre-homogenization pile after grinding raw mix to fine powder.Cement manufacturing process phase iii pre-heating raw material.After final grinding, the material is ready to face the pre-heating chamber.Pre-heater chamber consists of series of vertical cyclone from where the raw material passes before facing the kiln.
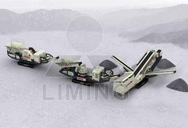
Cement Raw Material | Loesche
Cement Raw Materials. The coordinates of the grinding table diameter and number of rollers can be read off from the table. The x-coordinate indicates which product throughputs can be generated using the respective mills. The width of the fields is a measurement of the output factor.
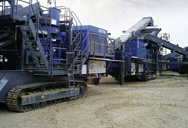
cement raw material grinding mill table - DUSTRI …
cement raw material grinding mill table. Raw Material Vertical Roller Mill is a type of industrial equipment used to crush or grind materials into small particles Our raw materials vertical roller mills are widely used in the concrete and mining fields and are also used to process gypsum. Chat Online . Cement Raw Material Loesche. Cement Raw Materials The coordinates of the grinding table ...
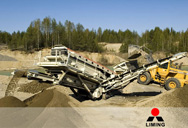
Raw Mill Grinding Table Segment Of Polysius
Vertical Raw Mill Cement Industry Polysius. Raw mill grinding table segment of polysius grinding trends in the cement industry cement lime gypsum 23 raw material mill 4800 in china hcrdi clinkercement grinding is the biggest market segment with 42 followed by raw material grinding with 34 polysius has implemented a similar concept eg at txi oro grande with the more details
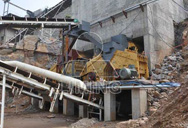
How To Maintain The Cement Raw Material …
Raw mill is also called raw material mill, which is the essential equipment in the production process of cement. It has large application such as raw mill in cement plant, building materials, metallurgy, electric power and stone industry, which is mainly used for the grinding as well as drying of cement raw materials and other materials.
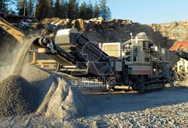
Raw Material Drying-Grinding - Cement Plant …
Ball Mill Ball mills with high efficiency separators have been used for raw material and cement grinding in cement plants all these years. Ball mill is a cylinder rotating at about 70-80% of critical speed on two trunnions in white metal bearings or slide shoe bearings for large capacity mills. Closed circuit ball mill with two compartments for coarse and fine grinding and a drying compartment with lifters are generally found in cement plants …
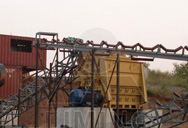
FOR CEMENT RAW MATERIAL - Loesche
Cement raw material has been almost exclusively ground in roller mills (vertical air-swept grinding mills) since the sec-ond half of the 20th century. Loesche was and is the pio-neer of this technology. Hundreds of Loesche mills have been used in the cement industry across the world to the present day. They operate with two, three, four and six roll -
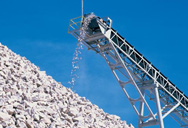
Raw Material Ball Mill
This ball mill is mainly used for grinding raw materials and final products in cement plant. It can be replaced by vertical raw mill. It is also suitable for grinding various ores and other materials in the metallurgy, mine, chemical, construction and other industries. Besides, the raw mill has two forms of milling, one is an open form, and the other is a recycle close form equipped with powder …
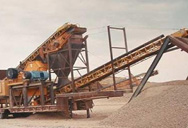
Rawmill - Wikipedia
A raw mill is the equipment used to grind raw materials into "rawmix" during the manufacture of cement. Rawmix is then fed to a cement kiln, which transforms it into clinker, which is then ground to make cement in the cement mill. The raw milling stage of the process effectively defines the chemistry (and therefore physical properties) of the finished cement, and has a large effect upon the efficiency …
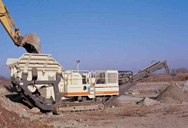
Energy-Efficient Technologies in Cement Grinding …
23.10.2015 · They are used in grinding of cement raw materials (raw meal) (i.e. limestone, clay, iron ore), cement clinker and cement additive materials (i.e. limestone, slag, pozzolan) and coal. Multi-compartment ball mills are relatively inefficient at size reduction and have high specific energy consumption (kWh/t). Typical specific energy consumption is 30 kWh/t in grinding of cement. liming …
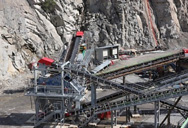
CEMENT MANUFACTURING PROCESS: RAW …
Dry grinding requires approximately 30 % more energy / wt. of ground material. Dry mills need more mill volume than comparable wet mills. However, the increased metal wear of the grinding media and the mill liners for wet grinding, equalizes the additional energy costs of dry grinding procedures ~ 30 - 40 % of wear costs in wet grinding.
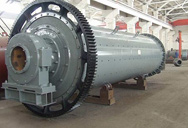
Our vertical roller mill offers optimum raw, …
Our best-in-class OK™ Mill is a globally successful vertical roller mill solution for grinding raw material, cement and slag. Its cutting-edge design features consistently deliver the highest quality products with the greatest efficiency. It is affordable to install and cost effective to operate over your cement plant’s lifetime.
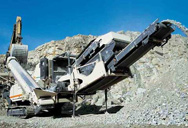
Large cement mill and raw material mill hot spot …
Cement mill and raw material mill because of different grinding materials, its hot spots are also different.Cement grinding because of grinding clinker temperature is generally higher (especially in summer), hot spots are grinding tail spindle tile and main reducer shaft tile;Due to the use of hot air from the humidifying tower at the end of kiln as the drying heat source, the hot spots are the sliding shoe …
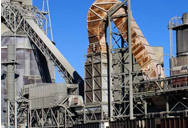
Modeling and Optimization of Cement Raw …
Cement production will experience several procedures which include raw materials blending process and burning process, cement clinker grinding process, and packaging process. Cement raw material and cement clinkers mainly contain four oxides: calcium oxide or lime (CaO), silica (SiO2), alumina (Al2O3), and iron oxide (Fe2O3).
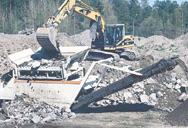
cement raw material grinding mill table - …
cement raw material grinding mill table. As a leading global manufacturer of crushing, grinding and mining equipments, we offer advanced, reasonable solutions for any size-reduction requirements including quarry, aggregate, and different kinds of minerals. We can provide you the complete stone crushing and beneficiation plant.We also supply stand-alone crushers, mills and beneficiation ...
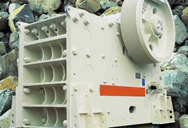
Coal mill, gypsum mill, clay mill, etc. | Pfeiffer MPS …
The grinding elements are primarily made of alloy cast iron as per DIN 1695, hardfaced cast iron or composite materials with high-chromium inserts in ductile base materials. The housings and other mill components are protected against jet wear with highly wear …
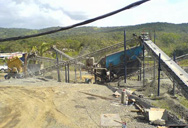
IMPROVING THERMAL AND ELECTRIC ENERGY EFFICIENCY AT …
1.1 Raw Material Preparation ..... 1 1.2 Fuel Preparation ... 2.5.3 Optimizing the Operation of a Cement Mill ..... 30 2.5.4 High-Pressure Roller Press as a Pre-grinding Step for Ball Mills ..... 31 2.5.5 Improved Grinding Media for Ball Mills ..... 32 2.5.6 High-Efficiency Classifiers..... 33 2.5.7 High-Efficiency Fans for Cement Mill Vents ..... 34. ii Improving Thermal and Electric Energy ...